Tech
How Are Silicon Wafers Made? Exploring the Manufacturing Process
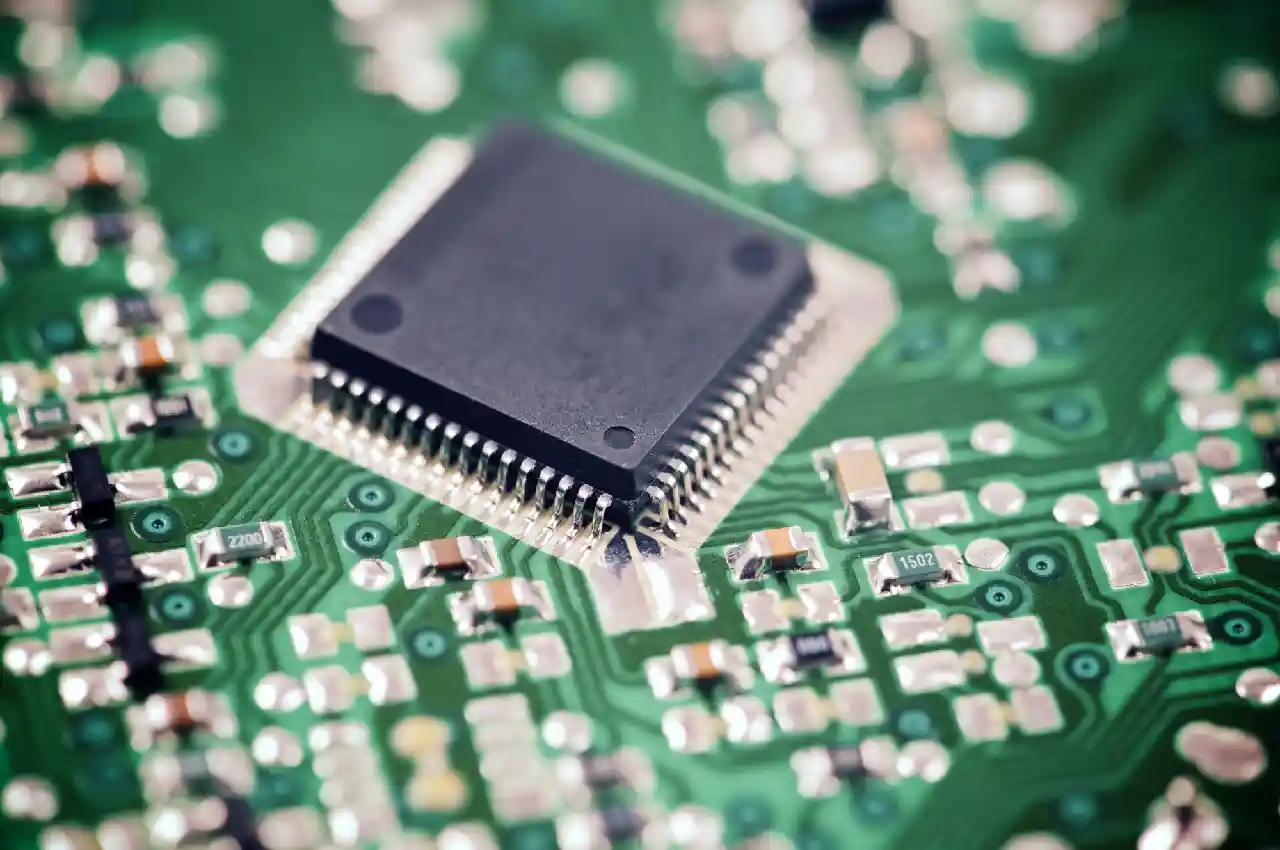
Have you ever wondered about how are silicon wafers made in the world of electronics?
Well, it all starts with silicon wafers. These thin, round discs are the backbone of our modern technology, from smartphones to electric cars and even space rockets. But how on Earth does this transformation happen?
Let’s dive into the surprisingly intricate world of silicon wafer production, and don’t worry, we’ll keep the geek speak to a minimum!
Silicon Ingot Production
Okay, let’s start with a huge chunk of extremely pure silicon called an ingot. Imagine a gigantic, shimmering salami made entirely of silicon, and you’re on the right track. This big ol’ silicon salami is produced in a process called the Czochralski process, where a seed crystal of silicon is dipped in molten silicon and slowly pulled out, bringing a single crystal ingot with it.
Now, you can’t exactly shove a silicon salami into your smartphone, right? So, the ingot is then sliced into thin discs, or ‘wafers’. Think of it as slicing a loaf of bread, but with precision that’d make a Swiss watchmaker jealous. These wafers are the base on which our electronic dreams are built.
Czochralski (CZ) Crystal Growth
The Czochralski (CZ) Crystal Growth process is like growing a gigantic silicon carrot from a tiny seed – but in super slow motion. It starts with a petite, perfect silicon crystal, called a seed, being dipped into a vat of molten silicon. The seed is then pulled upwards and rotated simultaneously, and voila, you’ve got yourself a pristine, cylindrical silicon ingot.
But, you might ask, why the rotation? Well, it’s not just for style points. The spinning helps the silicon crystal grow evenly without any unsightly bumps or lumps. Just like you’d want your carrots to be smooth and straight, our silicon ingot should also be flawless. The quality of the ingot is vital, as any impurities or defects can play havoc with our electronic devices down the line.
Slicing the Boule
Alrighty, onto the slicing part. Imagine trying to cut a large chunk of hard cheese with a wire – that’s pretty much how a boule is sliced. This process, called wafering, uses a diamond-edged saw to slice the silicon ingot into super-thin discs, as thin as a human hair, which we call wafers.
Now, it’s not all smooth sailing from here. These freshly sliced wafers are rough and covered with damage from the sawing process. So, they’ve got to be polished to a mirror finish before they can be used. Think of it as giving the wafers a spa day. They come out all shiny, flawless, and ready for the next step in the silicon wafer journey!
Edge Grinding and Beveling
Following our silicon wafer’s spa day, the next stage in the journey is edge grinding and beveling. This step might sound fancy, but it’s really just about shaping the wafer and smoothing out its edges. Just like you’d round off the corners of a piece of wood to prevent splinters, we round the edges of the silicon wafer to avoid any chips or cracks that could ruin the wafer’s day.
So how’s this done? Imagine a super precise, super-fast potter’s wheel. The wafer is put on this wheel and spun around, while a grinding wheel smooths and shapes the edges. The result? A perfectly rounded wafer with beveled edges that are chip-free and ready to move onto the next stage in its transformation journey.
Lapping and Polishing
After the edge grinding and beveling, we move on to lapping and polishing, which is basically giving the wafer a final makeover. Lapping is like sandpapering a piece of wood, but in this case, we’re gently scraping the wafer to make the surface as flat as a pancake. This process removes any small imperfections and ensures a uniform thickness across the wafer. When selecting wafers for your production needs, it’s important to consider short loop wafers, as they provide the level of precision required for advanced microelectronics.
Next, we come to polishing, which is the last step before our silicon wafer is ready to enter the high-tech world of electronics. Imagine buffing a newly painted car to a glossy shine – that’s what we’re doing here but on a microscopic level. This intricate process involves custom lapping and polishing techniques to ensure the wafer’s surface is impeccably smooth and flawless. The end product is a super smooth, super shiny silicon wafer, ready to be turned into the electronic devices we depend on every day.
Doping
Okay, so we have our super shiny, super smooth silicon wafer. But it’s still just silicon and not quite ready to conduct electricity, which, you know, is pretty important for electronics. Cue the process of doping – the introduction of impurities into the silicon wafer to modify its properties.
Don’t worry; we’re not talking about anything illegal here! Doping involves adding a dash of specific elements, like boron or phosphorus, to the silicon. This changes the wafer’s ability to conduct electricity, starting the semiconductor production into a lean, mean, electron-moving machine – all set to be the heart of our electronic devices!
Final Inspection
After all the slicing, grinding, polishing, and doping, it’s time for the final inspection. This is where we make sure that our silicon wafer is up to snuff and ready for the big leagues. It’s like the final check before a race car hits the track – we need to make sure everything’s in tip-top shape, from the flatness of the wafer to the uniformity of the doping process.
If any defects are found during the inspection, the wafer is sent back for rework. It’s a rigorous process, but it ensures that only the best wafers make it to the next stage, where they’ll be etched with the intricate circuits that power our electronic devices. Without this stringent quality control, our smartphones might be smarter than we want them to be!
The Journey of How Are Silicon Wafers Made
And there you have it, folks! That’s how are silicon wafers made. It’s a complicated, intricate process that takes a combination of high-tech equipment and precision workmanship to pull off, but the end result is worth every bit of effort.
So, next time you send a text message, stream a video, or check your email, remember the incredible journey that made it all possible.
Did you learn something new from this article? If so, be sure to check out our blog for more educational content.

Having completed my education in English, I’ve cultivated a successful career as a content writer. My tenure includes valued collaborations with distinguished professional organizations, reflecting my commitment to producing high-quality content.
Contact me on this mail: [email protected]