Business
Tips for Implementing Work Order Management Software in Your Organization
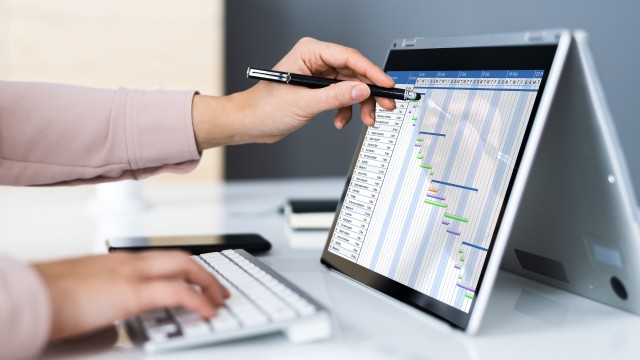
In the dynamic landscape of today’s business world, organizations are consistently seeking methods to optimize their operations and enhance overall efficiency. One area that often requires attention is work order management. Managing work orders effectively is essential for maintaining productivity and reducing downtime. Fortunately, with the advent of work order management software, also known as Computerized Maintenance Management Systems (CMMS), businesses now have a powerful tool at their disposal.
In this blog post, we will discuss five valuable tips to help you successfully implement work order management software in your organization and optimize your maintenance processes.
5 Proven Tips for Implementing Work Order Management Software in Your Organization
The following five proven tips will help you successfully implement work order management software in your organization:
Tip #1: Define Your Goals and Objectives
Before diving into any software implementation, it’s crucial to define your organization’s goals and objectives. Determine what you want to achieve by implementing work order management software. Are you looking to reduce downtime, increase equipment lifespan, or improve response times? Clearly defining your goals will help you choose the right software solution and align your team’s efforts toward a common objective.
Tip #2: Conduct a Needs Assessment
Performing a thorough needs assessment is an essential step in selecting the most suitable work order management software for your organization. Identify the pain points and challenges your maintenance team faces. Do you need help with high work orders, lack of communication, or inefficient scheduling? Understanding your specific needs will enable you to choose a software solution that addresses those pain points and provides the necessary features and functionalities.
Tip #3: Involve Key Stakeholders
Implementing work order management software requires buy-in from key stakeholders within your organization. Engage with maintenance managers, technicians, and other relevant departments to ensure their requirements are considered during the selection and implementation process. Involving stakeholders early on fosters a sense of ownership and increases the likelihood of successful adoption.
Tip #4: Provide Adequate Training and Support
To maximize the benefits of work order management software, you must provide comprehensive training and ongoing support to your team. Conduct training sessions to familiarize users with the software’s functionalities, workflows, and best practices. Additionally, offer ongoing support to address any questions or concerns that arise. This will help your team embrace the software and ensure a smooth transition to the new system.
Tip #5: Start with a Pilot Project
If you have a large organization or a complex maintenance operation, consider starting with a pilot project before rolling out work order management software across the entire organization. Select a representative sample of equipment or a specific area to test the software’s effectiveness and gather feedback. This approach allows you to identify and resolve any potential issues on a smaller scale before scaling up to the entire organization.
Conclusion
Implementing work order management software, also known as CMMS, can revolutionize your organization’s maintenance operations. By following these tips you can successfully integrate work order management software into your organization. Embrace the power of work order management software and experience enhanced productivity, streamlined workflows, and improved maintenance efficiency.
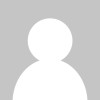
Umar Nisar was born and raised in the busy city of Abbottabad. As a journalist, Umar Nisar has contributed to many online publications including PAK Today and the Huffing Post. In regards to academics, Umar Nisar earned a degree in business from the Abbottabad UST, Havelian. Umar Nisar follows the money and covers all aspects of emerging tech here at The Hear Up.
Thanks