NEWS
Preventing Downtime: The Cost of Neglecting Heavy Equipment Repairs
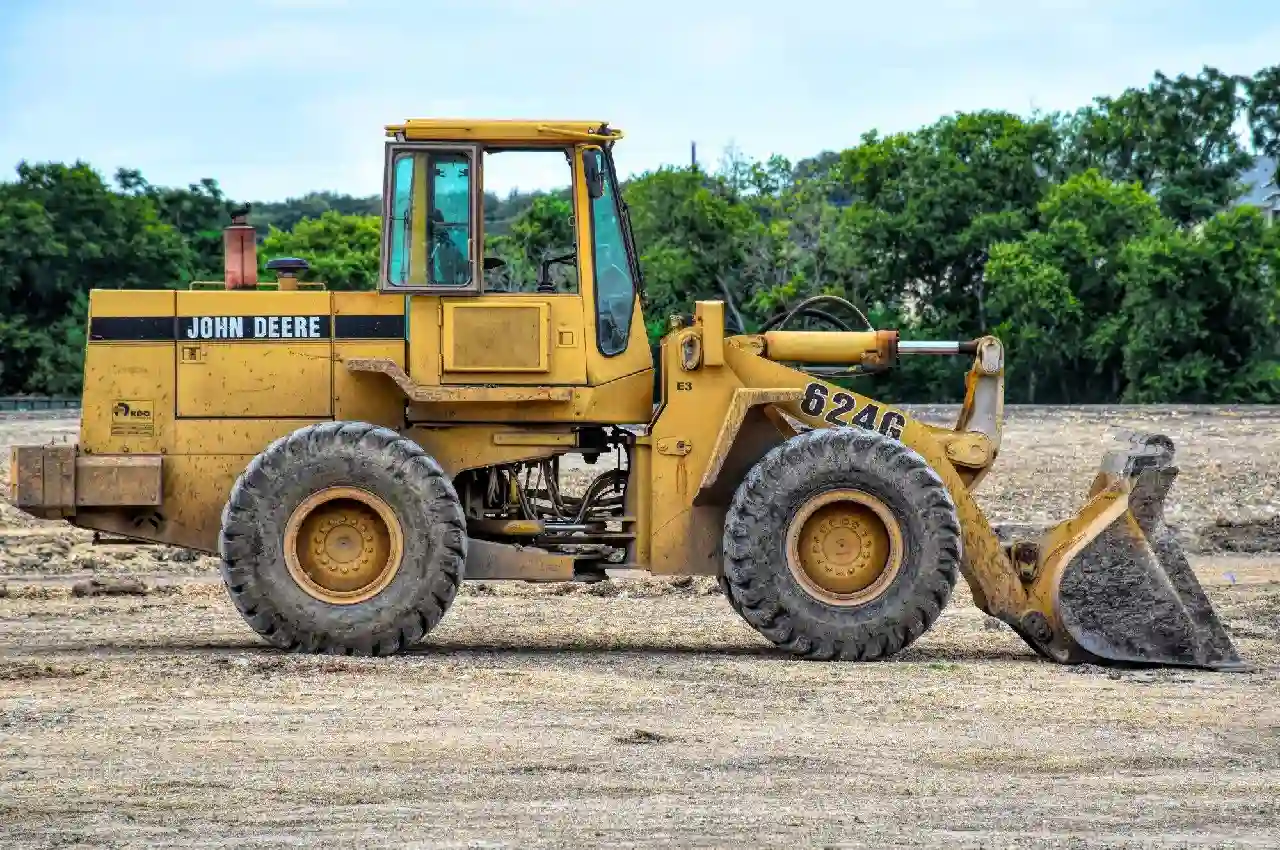
In the world of heavy industry, equipment isn’t only a necessary cog in a well-oiled machine-it is the machine. From construction to manufacturing, each piece of heavy equipment represents a massive investment. It impacts productivity, safety, and the bottom line.
With delayed maintenance, the cost of avoidance can be crippling. Here are the top reasons why you cannot afford to neglect those heavy equipment repairs.
Deferred Maintenance: A Risky Strategy Leading to Catastrophic Breakdowns
Delaying needed heavy construction equipment repair is like playing a risky game. Such machines face heavy loads and harsh conditions. People use them for long periods without proper care. So, they are vulnerable to wear and tear.
This neglect can precipitate sudden and costly failures. Vehicles can have blown engines leaving you stranded at the worst time. To serious hydraulic malfunctions in machinery that can halt production lines.
The repercussions of such breakdowns are immediate and severe. It causes operational disruptions and financial strain. This is because of the unexpected repair costs and loss of business during the downtime.
The High Cost of Downtime: Its Impact on Your Profit Margins
Every hour of downtime due to breakdowns hurts the timeline and the budget. The financial impact of equipment downtime varies across different industries.
But it can accumulate to thousands of dollars in lost revenue per hour. Not to mention the potential damage to customer relationships and future business opportunities.
Regular maintenance is the best way to reduce big, but preventable, financial losses. Proactive maintenance preserves machinery’s functioning and cuts the chance of failures.
Skyrocketing Safety Risks Due to Compromised Equipment Integrity
The consequences of mechanical failures extend beyond financial losses and operational inconvenience. They pose serious safety hazards that can endanger lives.
Imagine a forklift with compromised brake functionality. Or a crane operating with a worn-out load-bearing cable. This can expose workers to risks of injury or worse, may lead to catastrophic accidents.
Keeping all equipment in great condition is key. It protects your most invaluable asset: your workforce.
Regular, comprehensive safety inspections and maintenance are crucial in preventing accidents. It helps maintain a safe work environment. Thereby fostering a culture of safety and responsibility among employees.
Regulatory and Compliance Issues: Adding Complexity to Repair Delays
In the heavy industry, navigating through bureaucratic red tape is a minor inconvenience. It’s a significant aspect of the day-to-day operational landscape.
When you delay maintenance and heavy machine repair, the risk increases. It may cause breaking key safety and environmental rules. Such violations invite legal complications.
It also risks damaging the company’s reputation. It may harm its reliability in the eyes of customers and regulators. Consequences can range from hefty fines to forced shutdowns that can disrupt operations.
So, timely maintenance and strict adherence to rules are vital. They avoid these issues and keep operations smooth. Establish a regular maintenance schedule and stay informed about changing regulations. Doing this can help navigate such challenges.
Productivity Stagnates With Diminished Equipment Capacity
Heavy equipment is important for various industries. It can face a drop in efficiency which happens when it is not operating at full capacity.
This decline often stems from faults or overlooked maintenance schedules. This can result in operational inefficiencies.
The delays in project completion could lead to missed opportunities for more work. This can impact the competitiveness of your business in the market.
Maintaining equipment to high standards not only ensures optimal performance. But, it also enhances your ability to meet demands. This can set you apart from competitors who may neglect such upkeep.
Regular checks and maintenance are paramount to keep machinery in prime working condition. This will safeguard your operational success in the long run.
Quality Control Wavers in the Face of Poor Equipment Conditions
Operating with faulty equipment leads to inconsistent work. This equipment is often compromised or in poor condition.
This inconsistency can increase the potential for errors, necessitating rework. This, in turn, could mean sacrificing customer satisfaction. You could also be losing out on lucrative contracts in the long run.
Maintaining a high standard of quality control is crucial for business success. Remember, the condition of the equipment used affects a project’s success.
A strict maintenance schedule ensures equipment is always in top condition. By maintaining and watching equipment, businesses can address issues before they get worse. This fosters a culture of reliability and excellence.
Asset Investments Depreciate Fast Without Proper Upkeep
Heavy equipment represents a significant capital investment for the construction or manufacturing sectors. Neglecting the maintenance of these assets speeds up their loss on the balance sheet. It also hampers the business’s ability to recoup value upon resale or trade-in.
Proper upkeep is essential to maintain the value of these assets over time. It ensures they contribute to the company’s financial health and operational capabilities. Regular maintenance and timely repairs safeguard against rapid depreciation, protecting your investment.
The Long-Term Health of Your Equipment Compromised
Designers create each key part of heavy equipment, to last for a specified lifespan. To get the most life out of Hyundai heavy equipment parts, for example, inspect them on a regular basis. They are key to finding early signs of wear and tear. Timely repairs and proactive maintenance help extend the life of these parts.
When you neglect routine maintenance, the lifespan of these parts is much shorter. This leads to a cycle of frequent replacements raising the business’s capital spending.
This affects the equipment’s efficiency and hurts productivity. Also, the company’s long-term financial planning is at risk. This is due to unforeseen expenses from equipment failures.
By doing proactive maintenance, businesses can ensure their equipment lasts and stays healthy. This plan reduces the risks of frequent breakdowns and protects the finances. Investing in equipment maintenance is important for effective operation and long-term financial health.
Avoid The Cost of Neglecting Heavy Equipment Repairs
In the business of moving mountains, you can’t be lackadaisical about equipment. It’s an investment in the heart of your operation, your people, and your future.
Prioritizing heavy equipment repairs isn’t only about ticking a box on a checklist. It’s a vital strategy for reliability, safety, and sustainability in the heavy industry.
Explore more insights and strategies on our blog. Delve into diverse topics that empower your industry knowledge and operational success.

Having completed my education in English, I’ve cultivated a successful career as a content writer. My tenure includes valued collaborations with distinguished professional organizations, reflecting my commitment to producing high-quality content.
Contact me on this mail: [email protected]