NEWS
How Does a Submersible Pump Work?
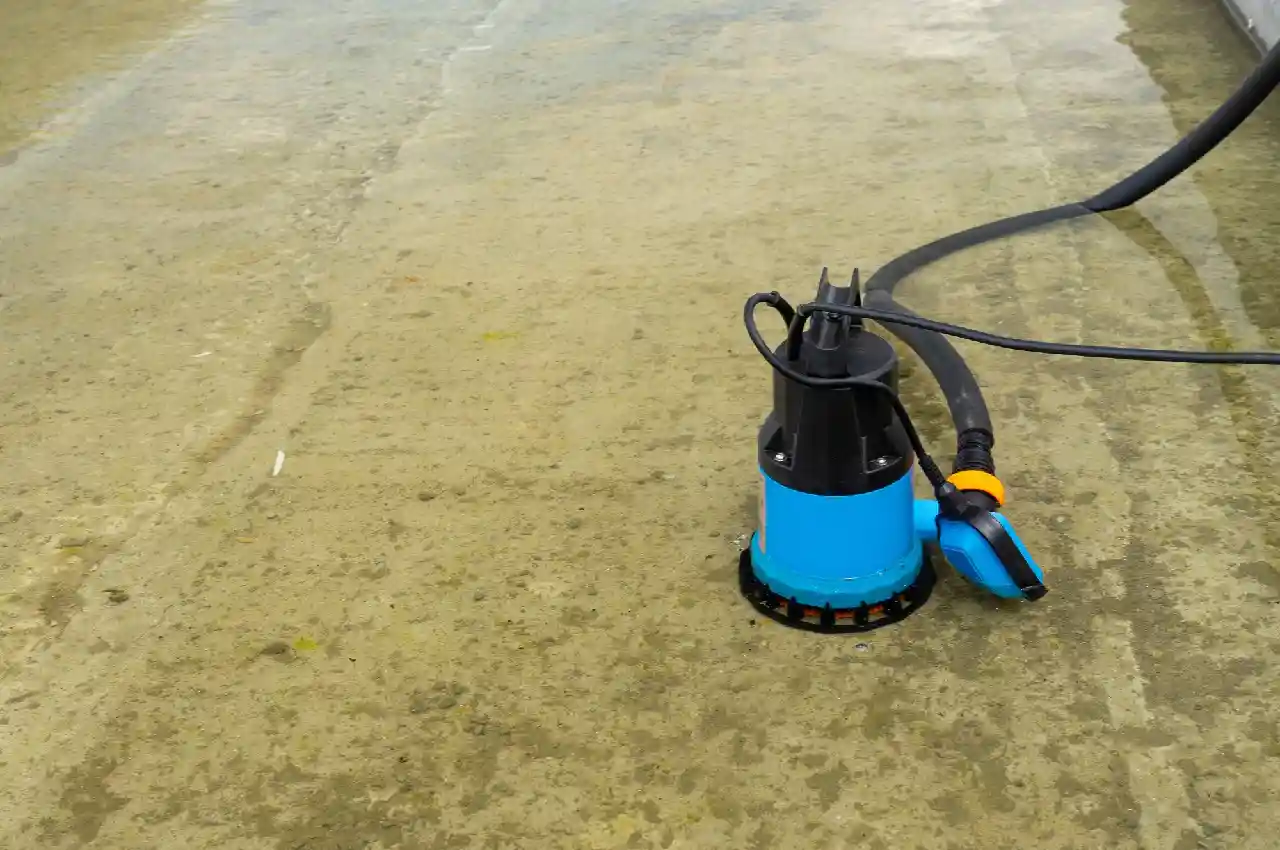
How does a submersible pump work? It’s a question that might not cross your mind when turning on a tap or watering your garden, but these submerged marvels play a vital role in ensuring water reaches our homes and fields.
In this article, we’ll dive into the depths of submersible pump technology, exploring the fascinating mechanics behind their ability to efficiently move water from beneath the surface to our everyday lives.
The Basics of Submersible Pumps
A submersible pump is a type of water pump designed to be fully submerged in the fluid it needs to move, whether it’s water from a well, a pond, or any other source. This pump is also used in a variety of industries, including those that generate electricity like a power plant, and can be referred to as an electrical submersible pump.
Unlike surface pumps that are placed above the water source and pull water up through a suction pipe, submersible pumps are placed underwater, where they push the water up to the surface. This unique design offers several advantages, including greater efficiency and a longer lifespan.
The Components of a Submersible Pump
A typical submersible pump consists of several key components that work together to move water effectively. These components include:
Motor
At the heart of the submersible pump is an electric motor. This motor is hermetically sealed to prevent water from entering and damaging it. The motor converts electrical energy into mechanical energy, which drives the pump’s impeller.
Impeller
The impeller is a rotating component with curved blades. It’s connected to the motor shaft and is responsible for creating the necessary force to move the water. As the impeller spins, it draws water in and then pushes it out with increased speed.
Diffuser
The diffuser is a stationary part of the pump that surrounds the impeller. Its job is to convert the kinetic energy produced by the impeller into pressure energy. Essentially, it slows down the flow of water and increases its pressure, allowing it to move upward.
Check Valve
To prevent water from flowing back down into the well or source when the pump is turned off, a check valve is often installed at the pump’s outlet. This valve only allows water to flow in one direction-upwards.
Cable
Since submersible pumps are placed underwater, they need a special waterproof cable to connect them to a power source on the surface. This cable is specially designed to withstand submersion and deliver electricity safely to the motor.
The Working Mechanism
Now that we’ve explored the key components of a submersible pump, let’s delve into the heart of the matter: how does a submersible pump work? In this section, we’ll delve deeper into the inner workings of these pumps.
Submersion and Seal
The journey of a submersible pump begins with its placement in the water source, often deep within a well or a borehole. One of the critical features of submersible pumps is their hermetically sealed design.
The entire pump, including the electric motor, is designed to be fully submerged without allowing any water to enter. This watertight seal is essential to protect the motor and ensure the pump’s longevity.
Activation of the Motor
When you flip the switch to turn on the submersible pump, electricity flows through the waterproof cable connected to the motor. This electrical current energizes the motor, setting the entire mechanism in motion.
Impeller Action
The heart of the submersible pump is its impeller, a rotating component with curved blades. It’s directly connected to the motor shaft, and as the motor spins, so does the impeller. The magic begins with the impeller’s action.
Creating Low Pressure
As the impeller rotates, it creates a low-pressure zone around itself due to centrifugal force. In simple terms, the impeller’s spinning motion generates a sort of vacuum effect. This low-pressure area has a critical role: it draws water into the pump.
Drawing in Water
At the bottom of the submersible pump, there is usually an intake screen or filter. This is where water from the surrounding environment is drawn in. The low-pressure zone created by the impeller’s action pulls water through this intake mechanism and into the pump.
The Role of the Diffuser
Once inside the pump, the water encounters the diffuser, which is a stationary component surrounding the impeller. The diffuser plays a crucial role in the process. It’s responsible for converting the kinetic energy generated by the impeller into pressure energy.
In simple terms, the diffuser slows down the flow of water and increases its pressure. It’s akin to squeezing a water hose nozzle to make the water shoot out with more force. The diffuser’s job is to pressurize the water, preparing it for the journey upward.
Water’s Upward Journey
With its kinetic energy converted into pressure energy by the diffuser, the water is now ready to move upward. It exits the pump through an outlet pipe. To ensure that water flows in only one direction-upwards-a check valve is often installed at the pump’s outlet. This check valve opens when the pump is running, allowing water to pass through, but it closes when the pump is turned off to prevent water from flowing back down into the well or source.
Overcoming Gravity and Resistance
The pressurized water now embarks on its upward journey, overcoming gravity and any resistance in the pipes along the way. This is where the submersible pump’s power becomes evident. It pushes water upward, against the pull of gravity, until it reaches the surface.
Delivery to the Surface
At the surface, the water exits the pump system and can be directed to its intended destination. In most cases, this means supplying water to our homes, gardens, irrigation systems, or other applications where pressurized water is needed.
Shut-off and Maintenance
When you turn off the submersible pump, the impeller stops spinning, and the flow of water ceases. Regular maintenance is essential to ensure the pump continues to operate efficiently. This includes checking and cleaning the intake screen or filter to prevent clogs and ensuring that all components remain in good working condition.
How Does a Submersible Pump Work
Understanding how a submersible pump works reveals the fascinating science behind its ability to efficiently deliver water from deep sources to our everyday lives. These submerged heroes play a crucial role in providing us with the water we need for domestic, agricultural, industrial, and many other essential purposes.
How does a submersible pump work? It’s the silent force beneath the surface that ensures water flows effortlessly into our world.
For more helpful articles, check out the rest of our website.

Having completed my education in English, I’ve cultivated a successful career as a content writer. My tenure includes valued collaborations with distinguished professional organizations, reflecting my commitment to producing high-quality content.
Contact me on this mail: [email protected]