Tech
Electrical Control Panels for Industrial Automation: Applications and Considerations
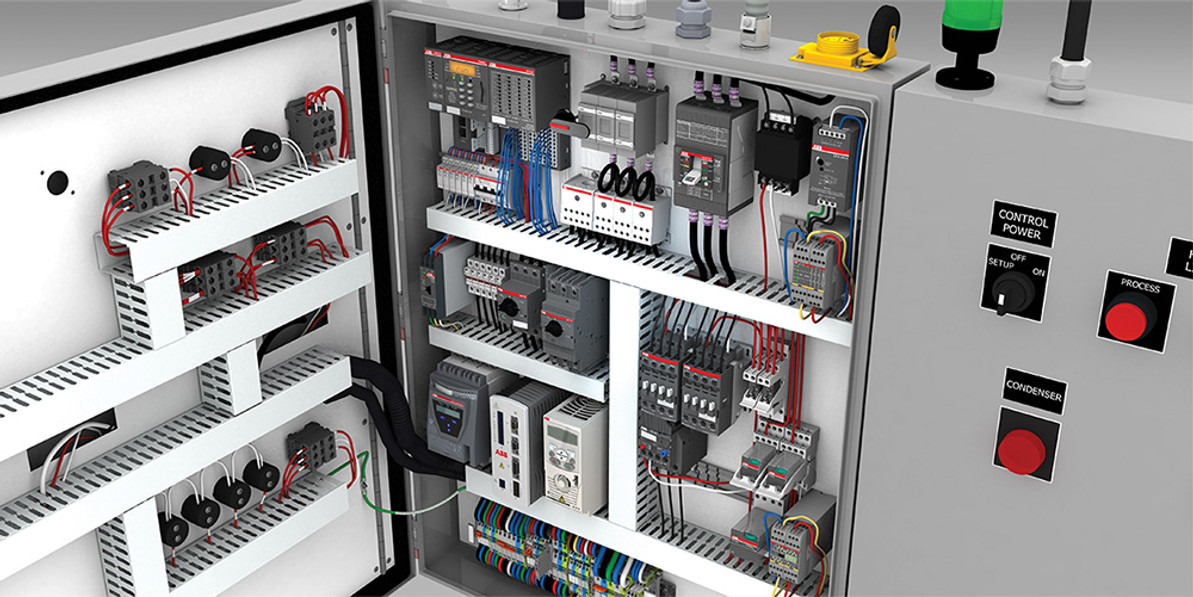
The world of electrical components is vast and varied, especially when we discuss automated electrical appliances. Each day, there is an innovation in the field of industrial automation. One such is the electrical control panel. Have you heard about this amazing piece of technological innovation? Well, these panels are a technical marvel that has instantly become an essential component of industrial automation processes. So, let’s find out what makes an electrical control panel so essential.
Application of an Electric Control Panel
These ingenious electric control panels are the brains of industrial automation. Panels help unit electrical components to control machinery and processes. From factories to power plants, they serve as the control centre, efficiently managing complex operations. The control panel directs different equipment like a traffic controller. It guides the flow of electricity to different parts of a building or a process. They bring all the electrical elements under one roof. As a result, this makes it easier to manage and control various functions. An electrical control panel is the control hub that makes things tick and operate smoothly in buildings, factories, and industries.
Key Components of Electric Control Panels
Beneath the complex exterior, these panels house a treasure of technical wonders. The below-mentioned components assist the electrical control panel in aligning electrical currents. As a result, it helps achieve desired outcomes within various industrial applications, mechanised systems, and operational processes.
- Circuit Breaker
It is a vital protective device that swiftly interrupts power flow in response to irregular current flow. Henceforth, assisting in the prevention of potential hazards and ensuring system integrity.
- Relays
These electromechanical switches serve as signal messengers by transferring commands between different components of the system with precision and accuracy.
- Timers
They are essential components for temporal control. Timers dictate the sequence and duration of specific operations, thus, enhancing synchronicity within the system.
- Contactors
Similar to electrical switches, they are efficient tools for the efficient management of the distribution and modulation of electrical currents.
- Programmable Logic Controller (PLC)
The core intelligence PLCs execute intricate algorithms, processing inputs, and generating outputs to execute seamless operations and programmed functions.
- Human-Machine Interfaces (HMIs)
They provide the means for operators to interact with and monitor the system, hence, offering crucial insights into the control process.
Considering Electric Control Panels for Industrial Automation
Industries have a plethora of activities that need to be done on a regular basis. From one thing to another, automation has been a helpful aid in making their operations seamless. Here are a few reasons why electrical control panels prove to be an effective consideration for effective industrial automation.
- Safety and Maintenance
Safety is paramount in any matter related to electricity. Therefore, ensuring adequate grounding, proper insulation, and effective protection against electrical hazards is essential. Besides, simplified access to these components and clear labelling make it easier and safer to operate with.
- Space Optimisation
Keeping in mind the idea of scalability, control panels organise the electrical components while optimising the space.
- Electromagnetic Compatibility (EMC)
These control panels are designed with ingenious technology so that they adhere to the EMC standards. As a result, it empowers the panel to protect the whole electrical system from any potential electromagnetic interference.
- Integration with Automation Systems
The task of integrating an automation system into control panels is as simple as it can be. What it does is incorporate the power of advanced technology, hence, enabling the user to make a much more informed decision.
Empowering Industrial Automation with Electrical Control Panels Now that you know all about how these electrical control panels make several industrial applications seamless, what stops you from using them? In fact, their future promises an even more profitable experience when incorporated with advanced automated systems. Find a trusted automation solutions company today and embrace the future of technology to automate your industries.

Kenneth is a proud native of sydney, born and raised there. However, he pursued his education abroad and studied in Australia. Kenneth has worked as a journalist for almost a decade, making valuable contributions to prominent publications such as Yahoo News and The Verge. Currently, he serves as a journalist for The Hear Up, where he focuses on covering climate and science news. You can reach Kenneth at [email protected].