NEWS
Discover the Different Types of Metal Coating
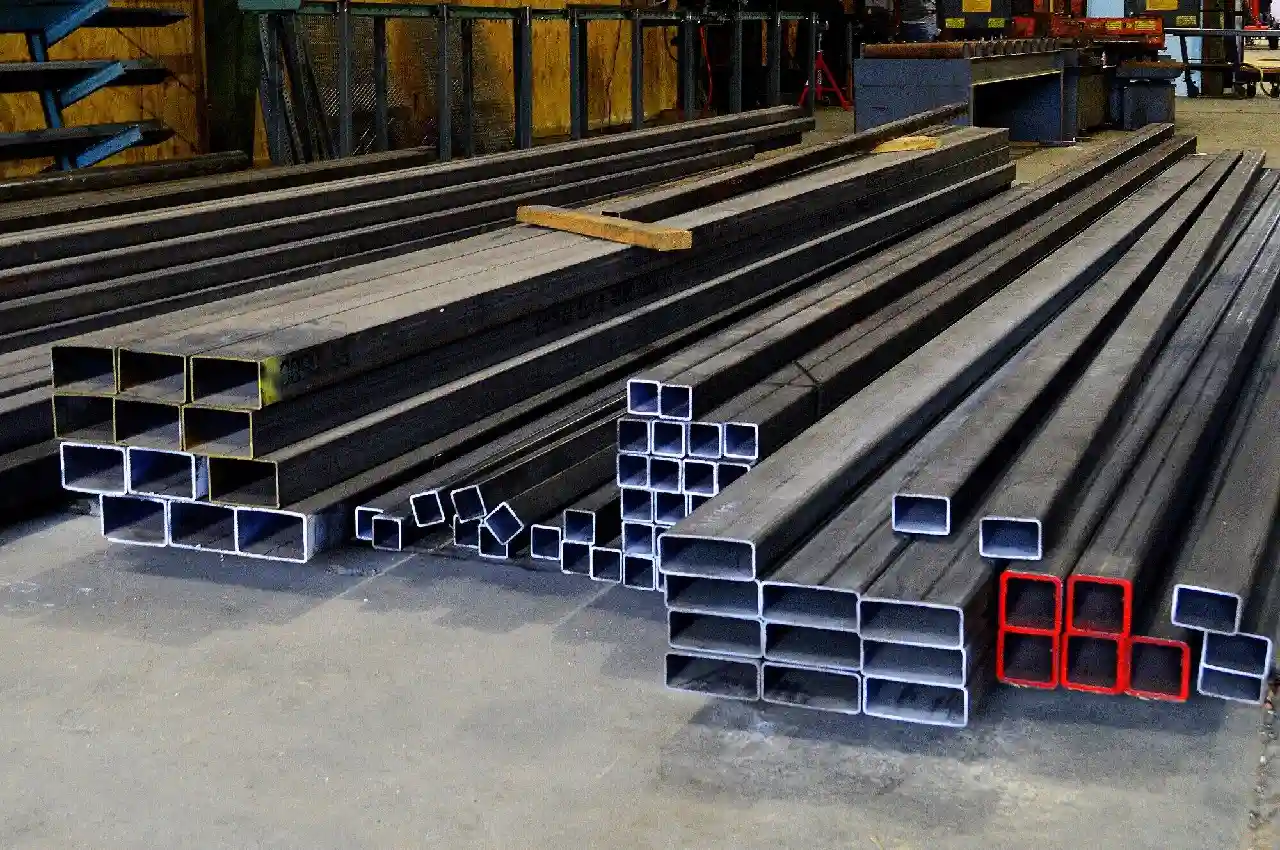
Have you ever wondered how metal objects keep their shine and don’t rust over time? The secret is in the metal coating! This protective layer not only keeps objects looking good but also makes them last longer.
Metal coating is everywhere – from the car you drive to the bridge you cross and the appliances in your home. In this article, we’ll explore the different types of metal coatings and how they work.
Get ready to discover the invisible shield that protects and enhances the metal items you use!
Galvanization
Galvanization is one process used to coat metals to protect them from rusting. It involves covering a metal, like iron or steel, with a thin layer of zinc. This zinc layer stops harmful elements like water and oxygen from reaching the metal underneath.
The process is really important for things that are used outdoors or in moist environments. It makes sure that metal structures, like bridges and fences, can last a long time without getting damaged by rust.
Powder Coating
Powder coating is a process where a powder material is applied to a metal surface and then heated to form a hard, protective finish. This method uses a powder consisting of pigment and resin, which is sprayed onto the surface and cured in an oven.
Unlike traditional liquid paint, powder coating does not require a solvent to keep the binder and filler parts in a liquid suspension form.
Electroplating
Electroplating is a process that uses electric current to reduce dissolved metal cations so that they form a thin coherent metal coating on an electrode. The main purpose of electroplating is to provide a decorative finish or to prevent corrosion of a metal.
In electroplating, the metal to be plated is submerged in a solution containing the metal ions. An electric current is then applied, causing the metal ions to move and deposit onto the surface of the submerged metal, creating a coating.
Anodizing
Anodizing is a process that increases the thickness of the natural oxide layer on the surface of metal parts. It is commonly used for aluminum to provide a more durable, corrosion-resistant finish. This technique involves immersing the aluminum in an acid electrolyte bath and passing an electric current through the medium.
This process not only enhances the metal’s durability but also allows for the metal to be dyed in various colors. It makes the surface of the aluminum harder and better protected against wear and tear.
Chem Film
Chem film, also known as chemical film coating, is a process applied to metals to protect them from corrosion. It involves applying a thin layer of chromate or phosphate to the metal surface. This layer helps in preventing rust and enhances the metal’s resistance to wear and tear.
When discussing chem film vs anodize, it’s important to note that both processes aim to increase a metal’s durability and resistance to corrosion. However, chem film is mainly used for its corrosion resistance properties, while anodizing also adds aesthetic appeal and the ability to dye the metal in various colors.
Shield Your Metal Marvels With Diverse Metal Coating Solutions
Protecting your metal items is crucial for keeping them in top shape for years. Thanks to various metal coating techniques, we can enjoy durable and beautiful metal objects in our daily lives, from cars to kitchen appliances.
By choosing the right metal coating, you ensure your metal treasures stay strong and look great, helping them last and serve us better.
We hope you enjoyed reading this article. If you found it helpful, be sure to check out our blog for more informative resources.

Having completed my education in English, I’ve cultivated a successful career as a content writer. My tenure includes valued collaborations with distinguished professional organizations, reflecting my commitment to producing high-quality content.
Contact me on this mail: [email protected]