Tech
8 Things to Look for When Buying Label Printers
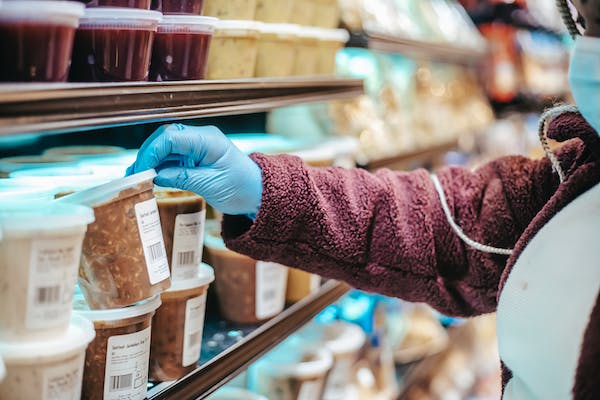
Choosing the right label printer for your business can be a difficult task. There are many aspects to consider when picking a label printer, including price and features. After all, with the right label printer, you get faster printing and better results. To help, here are eight things to consider before deciding on a label printer.
Budget
It’s important to decide how much you’re willing to spend on a label printers before making your decision. There are many models in the market, and you must decide which is best for you. A good label printer can easily print anything from small business cards to large signs. Depending on your needs, you may want to invest in a higher-end model with more features or save money with a lower-cost option with fewer features. Make sure the device meets all your requirements before making purchase decisions based on its price tag!
Media Compatibility
Media compatibility is another important thing to consider when choosing a label printer. There are laser printers and thermal printers, which use heat to print on paper. Inkjet printers, on the other hand, use ink sprayed onto paper. Each type of label printing has its advantages and disadvantages. Some printers are better suited for printing on certain materials, such as glossy or matte paper, while others may have difficulty with certain types of inks or coatings. Not all label printers can handle all types of media, so it’s important to ensure that the model you choose is compatible with your preferred media type (e.g., paper, vinyl, fabric). This will ensure that your labels look their best every time!
Printing Speed
Printing speed is essential when choosing a label printer, especially if you need to quickly produce large quantities of labels. A high-speed label printer will be a great investment for your business. It will help you to save time and money, as well as increase the efficiency of your production. You will want to choose a printer with a fast print speed so that it can handle large amounts of product at once without slowing down or interrupting production lines. The faster the printing speed, the less time you’ll have to wait for your labels to be finished.
Ink Type
Different types of ink and toner are available depending on the type of label printer you choose. Inkjet printers use liquid ink cartridges, while laser printers use toner cartridges filled with dry powdery toner heated and fused onto the paper by the printer’s fuser unit. Choose carefully, as each cartridge type will have its advantages and disadvantages, such as cost and output quality.
Connectivity Options
The connectivity options are also very important when choosing a label printer. Some printers offer only one connectivity option, while others have multiple options. It would be better to choose a printer that offers multiple connectivity options, so you do not have to worry about compatibility issues while using it. Consider whether the printer can connect to your computer or network via USB, Ethernet, or Wi-Fi. It will affect how easily you can print from different devices or locations. Some models may also offer cloud connectivity allowing you to print remotely from anywhere in the world via an internet connection!
Durability
A good label printer will last for years without any maintenance requirements. Look for a label printer that comes with a durable casing, as well as a long warranty period. The printer you choose should withstand the rigours of daily use, including drops, spills and other accidents that might occur in the warehouse or manufacturing facility. The durability can be checked by looking at the quality of materials used in manufacturing the product and the components used in its construction.
Printer Size
Another important consideration is whether you need mobile or industrial printing capabilities. Do you need a smaller printer for ease of transportation? Or do you require a large-format printer that can handle larger labels? The printer size you choose will determine the number of labels you can print at one time. Mobile printers are smaller and use less ink, so they’re great for printing small runs of labels. It’s suitable for smaller businesses and those who are on the go. The desktop printer is larger than a mobile printer and has more features. These printers are stationary, and you can place them against a wall or desk. On the other hand, industrial printers are often used for large-scale applications like packaging and shipping.
Maintenance Requirements
Last but not least, you should also keep an eye out for maintenance requirements when choosing a label printer. The maintenance requirements of each printer vary from model to model. Some models require regular cleaning of their motorised components and ink cartridges so they don’t become clogged with dust or dirt over time. However, if too many maintenance requirements are involved, it might be difficult for you or your employees to use and maintain it properly, which can lead to problems down the road.
Final Takeaway
As you can see, many factors are involved in choosing the right label printer for your business needs, from budget considerations and printing speeds to media compatibility and maintenance requirements. Researching each of these aspects will ensure that you purchase the best possible device for your labelling needs now and in the future!
DAL offers the best label printers in the industry to suit your requirements. They have a wide variety of options, including direct thermal label printers, zebra mobile label printers and much more. Get in touch with the professional team of DAL today!

Umar Nisar was born and raised in the busy city of Abbottabad. As a journalist, Umar Nisar has contributed to many online publications including PAK Today and the Huffing Post. In regards to academics, Umar Nisar earned a degree in business from the Abbottabad UST, Havelian. Umar Nisar follows the money and covers all aspects of emerging tech here at The Hear Up.
Thanks