NEWS
5 Uses for Professionally-Constructed Molded Foam
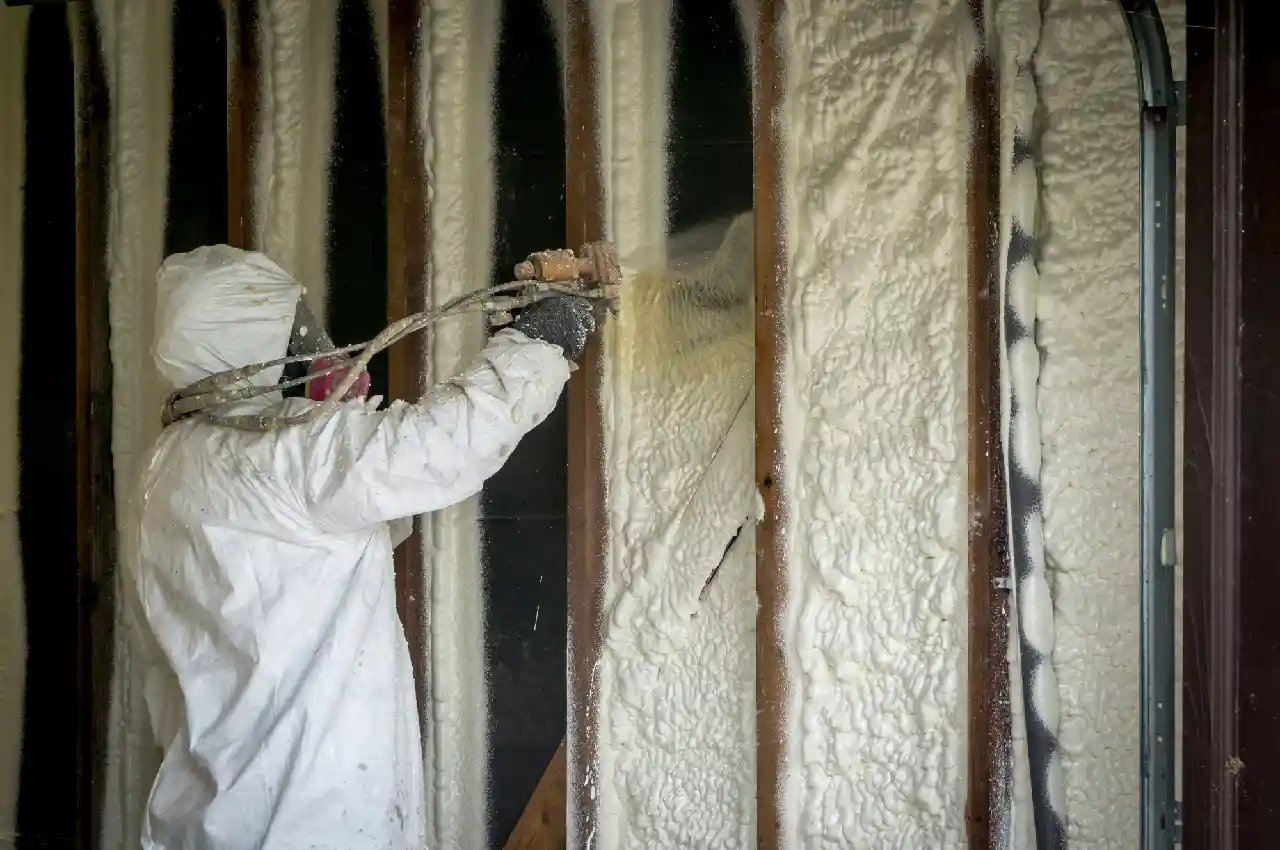
You wouldn’t think that something like a piece of construction foam would have such a wide range of uses. However, other than ones that are related to construction, there are plenty. For example, you can use mold foam as a comfortable seat, packaging, evidence handling, insulation, and much more.
If you’re interested in learning more about how mold foam can benefit you, then keep on reading for our top five.
1. Custom Cushions and Mattresses
Custom molded foam is exceptional for creating comfortable and durable cushions and mattresses. It is perfectly suited to accommodate body contours and is more stable than standard foam sheets.
It also offers more support with less weight, making it a great choice for custom cushioning projects. Additionally, it aids to reduce tossing and turning by providing stress-point support. These structural foams are also highly resistant to:
- Dust
- Bedbugs
- Bacteria
- Other allergens
All these factors make it a great choice for health-conscious households. Lastly, it can be used both indoors and outdoors, making it a versatile solution for all your cushioning needs.
2. Crafting Furniture Items
Molded foam is often used to craft everything from sofas and sectionals to seating cushions. They can be custom-cut into nearly any shape, allowing them to create an ideal fit for any type of furniture item.
It also works well for producing curved designs, which are popular in modern furniture trends. Finally, its durability makes it an ideal solution for long-lasting furniture pieces.
3. Custom Food Packaging
These moldable materials provide superior protection and insulation for food products. It can also be used to create a range of packaging shapes and sizes.
It is particularly useful for producing smaller packages or individual servings, as it can be easily formed into even the tightest shapes. Finally, it ensures items are kept safe from bumps or drops during transit.
4. Swim Floatation Devices for Recreational Activities
Molded foams are designed to provide superior buoyancy and maximum comfort. This makes it the perfect material for popular types of swim floatation devices such as:
- Swimming pool noodles
- Buoyancy vests
- Kickboards
- Armbands
- Life jackets
They range in size and design, depending on the age and size of the user. Ultimately, it can give much-needed assistance to those who are not yet strong enough swimmers to stay afloat on their own.
5. Soundproofing and Insulation
Another way to use molded foam is to soundproof a room. By creating a barrier between air pockets, it absorbs sound and prevents it from echoing off the walls, reducing noise levels significantly.
Its microcellular structure makes it ideal for insulation, thanks to its ability to block air, temperatures, and moisture. It can also be used to cushion walls, ceilings, and floors, preventing energy from being wasted through leaks or drafts.
As a result, it can help to improve the energy efficiency of residential or commercial spaces. Explore this page for more applications that molded foam has to offer.
The Great Benefits of Using Professionally-Constructed Molded Foam
Molded foam is an awesome tool for a variety of projects. Whether you’re creating custom shapes for decorations, organizing sports and work items, or crafting a life-like figure, this foam is the way to go.
So, why wait? Give your next project the amazing treatment with moldable materials today!
Did you find this article helpful? Check out the rest of our blog now!

Having completed my education in English, I’ve cultivated a successful career as a content writer. My tenure includes valued collaborations with distinguished professional organizations, reflecting my commitment to producing high-quality content.
Contact me on this mail: [email protected]